文章來(lái)源:學(xué)習(xí)那些事
原文作者:前路漫漫
本文介紹了晶圓減薄的各種技術(shù),著重詳細(xì)介紹了磨削減薄技術(shù)。
減薄的作用
在半導(dǎo)體制造流程中,晶圓在前端工藝階段需保持一定厚度,以確保其在流片過(guò)程中的結(jié)構(gòu)穩(wěn)定性,避免彎曲變形,并為芯片制造工藝提供操作便利。不同規(guī)格晶圓的原始厚度存在差異:4英寸晶圓厚度約為520微米,6英寸晶圓厚度約為670微米,8英寸晶圓厚度約為725微米,12英寸晶圓厚度約為775微米。盡管芯片功能層的制備僅涉及晶圓表面幾微米范圍,但完整厚度的晶圓更有利于保障復(fù)雜工藝的順利進(jìn)行。直至芯片前制程完成后,晶圓才會(huì)進(jìn)入封裝環(huán)節(jié)進(jìn)行減薄處理。
晶圓翹曲
封裝階段對(duì)晶圓進(jìn)行減薄主要基于多重考量。從劃片工藝角度,較厚晶圓硬度較高,在傳統(tǒng)機(jī)械切割時(shí)易出現(xiàn)劃片不均、裂片等問(wèn)題,顯著提升不良率;而減薄后的晶圓硬度降低,能夠?qū)崿F(xiàn)更精準(zhǔn)、高效的分離,大幅提升劃片質(zhì)量與效率。隨著電子設(shè)備向輕薄化方向發(fā)展,封裝厚度已成為關(guān)鍵指標(biāo),尤其在芯片堆疊技術(shù)中,晶圓減薄能夠有效降低整體封裝厚度,滿足可穿戴設(shè)備、移動(dòng)終端等微型電子產(chǎn)品的需求。同時(shí),晶圓制造過(guò)程中背面形成的氧化層會(huì)影響芯片鍵合質(zhì)量,減薄工藝可有效去除氧化層,為鍵合提供潔凈、平整的表面,確保電氣連接的可靠性。此外,減薄能夠縮短芯片工作時(shí)的熱量傳導(dǎo)路徑,加速散熱,避免因高溫導(dǎo)致的性能衰退與壽命縮短,提升芯片長(zhǎng)期運(yùn)行的穩(wěn)定性。
不同封裝結(jié)構(gòu)對(duì)晶圓減薄厚度的要求存在顯著差異。DIP封裝通常將晶圓減薄至約300微米;BGA封裝減薄范圍在120-250微米;而在先進(jìn)的疊層封裝中,芯片厚度甚至可薄至30微米以下,以滿足高密度集成需求。
在芯片切割環(huán)節(jié),傳統(tǒng)流程是先在晶圓背面粘貼藍(lán)膜并固定于鋼制框架(即晶圓黏片工藝),隨后采用機(jī)械切割或激光切割進(jìn)行分離。機(jī)械切割使用高速旋轉(zhuǎn)的金剛石磨輪刀片,但易在晶圓表面產(chǎn)生應(yīng)力導(dǎo)致崩裂;激光切割則通過(guò)聚焦激光在晶圓內(nèi)部形成變質(zhì)層,配合膠膜擴(kuò)展實(shí)現(xiàn)晶粒分離,顯著降低對(duì)硅片的損傷。
隨著工藝創(chuàng)新,“先劃片后減薄”(DBG)與“減薄劃片”(DBT)技術(shù)應(yīng)運(yùn)而生。DBG工藝先在晶圓正面切割出一定深度的切口,再進(jìn)行背面磨削;DBT技術(shù)則是預(yù)先形成切割切口,通過(guò)磨削減薄后利用ADPE腐蝕去除剩余材料,實(shí)現(xiàn)裸芯片自動(dòng)分離。這兩種方法有效規(guī)避了傳統(tǒng)工藝中減薄導(dǎo)致的硅片翹曲與劃片造成的芯片邊沿?fù)p傷問(wèn)題。其中,DBT技術(shù)憑借各向同性Si刻蝕劑,既能消除背面研磨損傷,又能修復(fù)芯片微裂與凹槽,大幅提升芯片抗碎裂性能。在此基礎(chǔ)上發(fā)展的DBG加DAF切割技術(shù),通過(guò)在DBG處理后的晶圓背面粘貼DAF(直接黏合膜),并對(duì)DAF進(jìn)行單獨(dú)激光切割,進(jìn)一步優(yōu)化了晶粒對(duì)齊精度,顯著提升加工質(zhì)量,成為先進(jìn)封裝工藝中的關(guān)鍵技術(shù)突破。
如圖所示,晶圓減薄到一定厚度后會(huì)像紙張一樣彎曲變形。
主要減薄技術(shù)
目前,硅片的背面減薄技術(shù)種類(lèi)多樣,主要包括磨削、研磨、干法拋光、化學(xué)機(jī)械拋光(CMP)、濕法腐蝕、等離子增強(qiáng)化學(xué)腐蝕(PECE)、常壓等離子腐蝕(ADPE)等方法。
硅片磨削工藝:該工藝通過(guò)砂輪在硅片表面旋轉(zhuǎn)施壓,使硅片表面經(jīng)歷損傷、破裂,最終實(shí)現(xiàn)材料移除,達(dá)到減薄目的。其顯著優(yōu)勢(shì)在于加工效率高,減薄后硅片平整度良好,且成本相對(duì)較低。然而,這種工藝也存在明顯弊端,磨削后的硅片表面會(huì)產(chǎn)生深達(dá)幾微米的損傷層,這不僅會(huì)降低器件的可靠性和穩(wěn)定性,還會(huì)在樣品表面殘留應(yīng)力,致使硅片發(fā)生翹曲。因此,通常需要后續(xù)工藝來(lái)消除損傷層和殘余應(yīng)力,以保證硅片的質(zhì)量。
硅片研磨工藝:硅片研磨工藝一般是指在低速條件下,使用松散研磨粉(膏)作為研磨劑進(jìn)行的多種表面精加工操作。經(jīng)過(guò)研磨后的硅片表面通常會(huì)呈現(xiàn)出微小的火山坑,表面灰暗而無(wú)光亮感。與磨削工藝相比,二者存在一些差異。磨削工藝壓力較大,研磨劑固定在砂輪上;而研磨工藝的研磨劑分布在研磨輪與樣品之間。此外,磨削工藝的材料去除速度比研磨更高。
化學(xué)機(jī)械拋光:綜合運(yùn)用機(jī)械、化學(xué)或電化學(xué)作用,通過(guò)降低工件表面粗糙度,得到光亮、平整的加工表面。該工藝屬于 “濕” 加工,使用精細(xì)的微米或亞微米磨料顆粒與液體,并利用襯墊容納磨料,拋光時(shí)材料去除量以微米為單位。它對(duì)工件預(yù)處理要求較高,需工件表面預(yù)先達(dá)到較低粗糙度,加工后能使樣品表面呈鏡面效果。雖然該工藝能有效改善晶圓表面平整度,減少表面缺陷,但存在加工效率低、成本高的問(wèn)題。
干式拋光技術(shù):原理與硅片磨削類(lèi)似,區(qū)別在于采用纖維和金屬氧化物制成的拋光輪替代金剛石砂輪。它可去除硅片磨削產(chǎn)生的損傷,實(shí)現(xiàn)納米和亞納米級(jí)鏡面加工,具有成本優(yōu)勢(shì)。不過(guò)其工藝效率較低,處理速度慢,更適合去除較淺的損傷層,在需要大量減薄材料的情況下難以發(fā)揮主要作用。
濕法化學(xué)腐蝕:通過(guò)腐蝕液與硅片發(fā)生化學(xué)反應(yīng)實(shí)現(xiàn)減薄,常用的腐蝕液有酸性體系,如硝酸、冰乙酸與氫氟酸混合液,以及堿性體系,如氫氧化鉀溶液。這種工藝的優(yōu)點(diǎn)是化學(xué)腐蝕后的硅片表面無(wú)損傷、無(wú)晶格位錯(cuò),有助于提高硅片強(qiáng)度,減少翹曲變形。但應(yīng)用時(shí)需要保護(hù)硅片正面,防止受到腐蝕液侵蝕,且對(duì)磨削條紋的校正能力較弱,限制了其在復(fù)雜表面處理場(chǎng)景中的單獨(dú)使用。
常壓等離子腐蝕:是一種在常壓下工作的純化學(xué)干式腐蝕技術(shù),以氬氣為環(huán)境氣體,將CF?氣體電離分解,硅片表面材料與氟發(fā)生化學(xué)反應(yīng)生成氣態(tài)SiF?,從而實(shí)現(xiàn)材料去除。該技術(shù)無(wú)需保護(hù)硅片正面,特別適合加工較薄硅片和帶有凸起結(jié)構(gòu)的硅片,能有效去除磨削損傷層,背面材料去除量可達(dá)50-100μm,加工后的表面平整性?xún)?yōu)于濕法化學(xué)腐蝕。然而,該技術(shù)設(shè)備成本較高,工藝參數(shù)控制要求也很?chē)?yán)格。
在實(shí)際晶圓減薄生產(chǎn)中,多采用組合工藝來(lái)確保加工精度與效率。例如,若需將硅片從初始的300μm減薄至120μm,可先通過(guò)高效的磨削工藝去除大部分材料,將硅片厚度削減至160μm左右。此時(shí),硅片表面因磨削產(chǎn)生損傷層與殘余應(yīng)力,就需要根據(jù)后續(xù)產(chǎn)品性能要求,從化學(xué)機(jī)械拋光、濕法化學(xué)腐蝕、常壓等離子腐蝕或干式拋光等工藝中,選擇一種或多種進(jìn)行精細(xì)處理。
常見(jiàn)的工藝組合方案有“背面磨削+化學(xué)機(jī)械拋光”“背面磨削+濕法化學(xué)腐蝕”“背面磨削+常壓等離子腐蝕”“背面磨削+干式拋光”。以“背面磨削+化學(xué)機(jī)械拋光”為例,前者快速去除大量材料,后者能有效降低表面粗糙度至納米級(jí),適用于對(duì)表面平整度要求極高的芯片制造;而“背面磨削+常壓等離子腐蝕”組合,在處理帶有復(fù)雜微結(jié)構(gòu)的超薄晶圓時(shí)更具優(yōu)勢(shì),既能高效減薄,又能保證結(jié)構(gòu)完整性。根據(jù)不同的產(chǎn)品需求與工藝標(biāo)準(zhǔn),靈活搭配這些組合方案,可實(shí)現(xiàn)晶圓減薄的高效化與高質(zhì)量化。
磨削減薄
磨削減薄技術(shù)憑借其高效的材料去除能力、優(yōu)異的表面平整度控制及相對(duì)經(jīng)濟(jì)的生產(chǎn)成本,成為晶圓減薄工序的核心技術(shù)方案。
1.硅片自旋轉(zhuǎn)磨削技術(shù)的迭代與創(chuàng)新
硅片減薄技術(shù)的發(fā)展歷程反映了半導(dǎo)體產(chǎn)業(yè)對(duì)加工精度與效率的持續(xù)追求。早期,旋轉(zhuǎn)工作臺(tái)磨削技術(shù)主要應(yīng)用于小尺寸硅片(直徑100mm以下)的背面減薄,但隨著硅片尺寸向大直徑發(fā)展,該技術(shù)在加工效率、厚度均勻性等方面的局限性日益凸顯。1988年,Matsui等人提出的硅片自旋轉(zhuǎn)磨削減薄技術(shù),為大尺寸硅片的超薄加工提供了新途徑。
該技術(shù)通過(guò)硅片的自主旋轉(zhuǎn)與研磨砂輪的協(xié)同運(yùn)動(dòng),實(shí)現(xiàn)了材料的高效去除與表面質(zhì)量的精確控制。以300mm硅片為例,當(dāng)原始厚度為750μm時(shí),采用硅片自旋轉(zhuǎn)磨削技術(shù),可在約90秒內(nèi)將其厚度減至180μm,厚度均勻性控制在±0.3μm以?xún)?nèi),表面粗糙度Ra可低至2-4納米,能夠滿足高端芯片制造對(duì)晶圓表面質(zhì)量的嚴(yán)苛要求。
然而,由于硅片邊緣倒角結(jié)構(gòu)的特殊性,在磨削過(guò)程中容易出現(xiàn)邊緣崩碎等缺陷。為解決這一問(wèn)題,TAIKO工藝應(yīng)運(yùn)而生。該工藝通過(guò)在晶圓工作臺(tái)邊緣設(shè)置特殊保護(hù)環(huán),在磨削時(shí)保留晶圓邊緣約3mm區(qū)域,有效增強(qiáng)了硅片的機(jī)械強(qiáng)度,降低了薄型晶圓的破損風(fēng)險(xiǎn),同時(shí)顯著改善了晶圓的翹曲變形問(wèn)題。
2. 磨削減薄工藝流程
1) 晶圓表面防護(hù)貼膜:在進(jìn)行背面研磨之前,對(duì)晶圓正面的精密電路與器件進(jìn)行保護(hù)至關(guān)重要。目前,行業(yè)普遍采用貼膜機(jī)完成晶圓貼膜操作。具體流程為:首先將晶圓正面朝上放置于貼膜機(jī)工作平臺(tái),隨后將保護(hù)膜從卷軸上平穩(wěn)拉出,覆蓋在晶圓表面,通過(guò)滾軸的均勻滾壓,使保護(hù)膜與晶圓表面緊密貼合,最后利用切割裝置沿晶圓邊緣將多余的保護(hù)膜切除,將完成貼膜的晶圓放入晶圓盒備用。
保護(hù)膜通常由膜層和膠層組成,膠層的黏性特性決定了其與晶圓表面的貼合效果。根據(jù)解膠方式的不同,保護(hù)膜可分為紫外線解膠型和熱解膠型等。紫外線解膠型保護(hù)膜在特定波長(zhǎng)紫外線照射下,膠層的黏性會(huì)迅速降低;而對(duì)于對(duì)紫外線敏感的集成電路產(chǎn)品,則需采用熱解膠型保護(hù)膜,通過(guò)加熱的方式實(shí)現(xiàn)解膠分離。
2) 背面研磨加工處理:完成貼膜的晶圓被轉(zhuǎn)移至研磨設(shè)備的陶瓷多孔真空貼片盤(pán)上,貼片盤(pán)通過(guò)真空吸附作用固定晶圓,并帶動(dòng)其高速旋轉(zhuǎn)。與此同時(shí),研磨砂輪在伺服系統(tǒng)的精確控制下,以設(shè)定的壓力與轉(zhuǎn)速對(duì)晶圓背面進(jìn)行研磨加工。
研磨過(guò)程分為粗磨和精磨兩個(gè)階段。粗磨階段使用大粒度砂輪,以較高的材料去除速率快速削減晶圓厚度;精磨階段則采用小粒度砂輪,對(duì)晶圓表面進(jìn)行精細(xì)研磨,進(jìn)一步降低表面粗糙度,提高表面平整度。通過(guò)粗、精磨的配合,能夠在保證加工效率的同時(shí),實(shí)現(xiàn)晶圓表面質(zhì)量的精準(zhǔn)控制。
3) 保護(hù)膜去除工藝:研磨完成后,首先對(duì)晶圓進(jìn)行清洗和干燥處理,以去除表面殘留的研磨碎屑和冷卻液。隨后,根據(jù)保護(hù)膜的類(lèi)型選擇合適的解膠方式。對(duì)于紫外線解膠型保護(hù)膜,通過(guò)特定波長(zhǎng)的紫外線照射,使膠層失去黏性;對(duì)于熱解膠型保護(hù)膜,則將晶圓加熱至一定溫度,實(shí)現(xiàn)膠層的軟化與分離。
解膠后的晶圓正面朝上放置于去膜設(shè)備平臺(tái),利用具有黏性的剝離膜將保護(hù)膜從晶圓表面揭除。為防止剝離過(guò)程中產(chǎn)生的靜電對(duì)晶圓造成損傷,整個(gè)操作過(guò)程需在離子風(fēng)環(huán)境下進(jìn)行。隨著晶圓厚度的不斷減薄,其機(jī)械強(qiáng)度下降,在加工過(guò)程中更易發(fā)生變形,因此在去膜過(guò)程中需嚴(yán)格控制操作力度與環(huán)境條件,確保晶圓的完整性。
-
芯片
+關(guān)注
關(guān)注
459文章
51988瀏覽量
434231 -
半導(dǎo)體
+關(guān)注
關(guān)注
335文章
28403瀏覽量
230610 -
晶圓
+關(guān)注
關(guān)注
52文章
5086瀏覽量
129046
原文標(biāo)題:晶圓減薄
文章出處:【微信號(hào):bdtdsj,微信公眾號(hào):中科院半導(dǎo)體所】歡迎添加關(guān)注!文章轉(zhuǎn)載請(qǐng)注明出處。
發(fā)布評(píng)論請(qǐng)先 登錄
硅片減薄技術(shù)研究
晶圓的基本原料是什么?
什么是晶圓測(cè)試?怎樣進(jìn)行晶圓測(cè)試?
晶圓凸點(diǎn)模板技術(shù)和應(yīng)用效果評(píng)價(jià)
硅晶圓是什么?硅晶圓和晶圓有區(qū)別嗎?
宜特晶圓:成功開(kāi)發(fā)晶圓減薄達(dá)1.5mil(38um)技術(shù)
單面晶圓減薄和處理研究報(bào)告
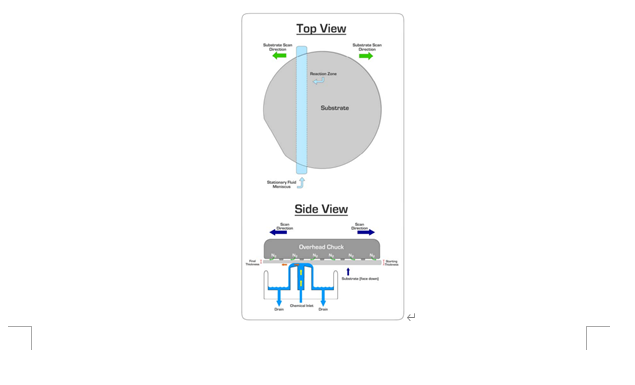
用于高密度晶圓互連的微加工晶圓減薄方法
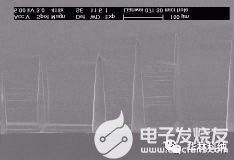
新開(kāi)發(fā)了一種GaN襯底減薄技術(shù)——激光減薄技術(shù)
半導(dǎo)體制造工藝超薄晶圓磨削減薄技術(shù)解析
簡(jiǎn)述晶圓減薄的幾種方法
陸芯半導(dǎo)體精密晶圓切割機(jī)領(lǐng)域發(fā)展趨勢(shì)及方向
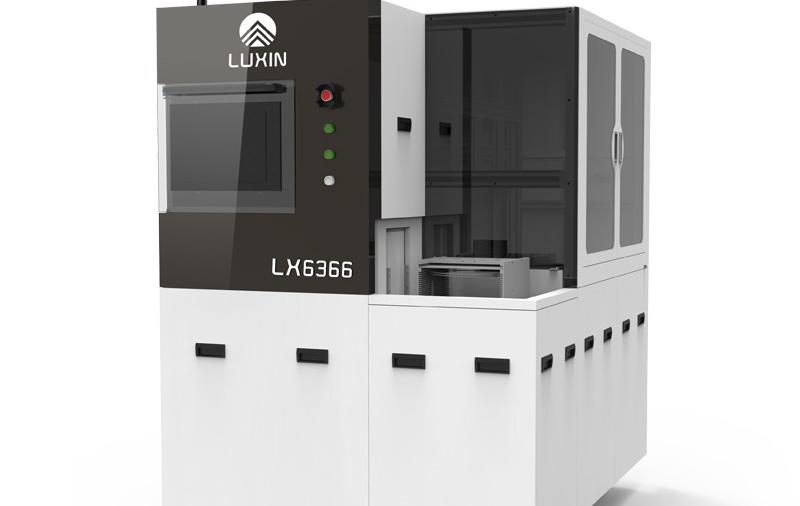
評(píng)論